1引言
在實際應用中,起重行業有很多起重機需要進行位置控制,例如全自動垃圾吊,電鍍車間的工作起重機;有些起重機對位置控制的精度要求還是比較高的,例如長軌焊接基地的軌道吊,核電實驗室的起重機等。
一想到位置控制,我們可能立刻想到的方案是使用伺服驅動器,當然伺服系統具有高精度,高反應速度等優點,但是對于起重行業來講,伺服驅動器的使用還是非常有限的,主要由于:
起重機的驅動功率通常比較大,伺服驅動器和變頻器相比,功率越大伺服驅動器的價格劣勢越明顯。
起重機的工作環境比較惡劣,通常會有灰塵,振動,高熱以及腐蝕等環境,會大大影響伺服驅動器的使用效果及壽命。
起重機對位置控制的精度通常不會太高,即便位置精度要求高,但其要求的反應速度一般比較低。
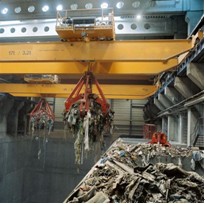
圖1 起重行業現場
綜上原因,我們完全可以在變頻控制器的基礎上開發位置控制系統,使用變頻器為驅動元件完成位置控制要求,這樣既提高了系統的可靠性,又大大降低了成本。
2系統控制要求
如圖2所示,在起重機的平移機構中,常見的驅動方式為變頻器驅動1到多個電機(典型值為1~6),由于是一拖多的方案,所以電機控制控制方式為開環。在起重機的起升機構中,驅動方式為變頻器一對一的驅動單個電機,所以電機控制控制方式為閉環矢量。
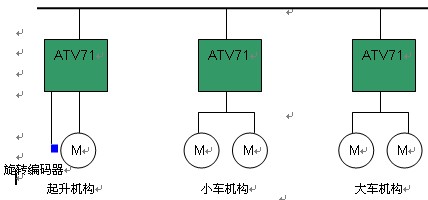
圖2 起重行業電機控制方式
平移機構由于是開環驅動,控制精度不高,而且平移機構的輪子和軌道之間還存在滑動,所以通常平移機構的位置精度要求誤差小于±20mm,要求較高的場合需要小于±5mm。
起升機構由于是開環驅動,控制精度高,沒有機械滑動,所以通常起升機構的位置精度要求誤差小于±5mm,要求較高的場合需要小于±1mm。
3系統解決方案
ATV71變頻器拖動一個電機進行FVC閉環控制,其位置精度完全能夠勝任起重應用場合,只是動態響應性沒有伺服系統高,但起重機不需要那么快速的響應速度。
3.1系統結構
通常我們要進行精確的位置控制,需要ATV71變頻器和電機做閉環控制,這就需要在電機上安裝旋轉編碼器,ATV71變頻器加裝編碼器卡和ATV-IMC卡。位置控制的主要運算和控制由ATV-IMC/CI卡來執行,系統結構圖如圖3所示。
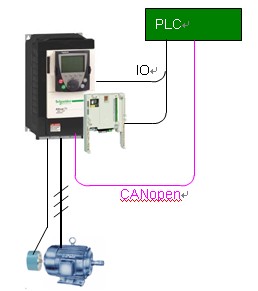
圖3 標準方案圖
位置控制的命令字以及位置給定等信息由PLC通過CANopen總線(也可以使用Modbus或以太網,如果使用以太網需在變頻器上加裝以太網卡)發送至ATV-IMC/CI卡,ATV-IMC/CI卡經過計算分析來驅動變頻器執行。安裝在電機軸上的旋轉編碼器既作為變頻器和電機之間的閉環速度檢測,也作為電機軸位置檢測的傳感器。
圖3為標準方案圖,位置檢測傳感器根據實際需要還可以直接和ATV-IMC/CI卡互聯。位置檢測傳感器除了旋轉編碼器,還有磁尺、格雷母線等。
3.2控制結構和原理
首先,在ATV-IMC/CI中位置控制的設計思路可以參考圖4的分析。

圖4 時間-速度曲線
按照圖4顯示,橫坐標為時間,縱坐標為速度,梯形的曲線為一段時間內物體的速度曲線,即加速,恒速和減速至0。這樣一個過程物體走過多遠的距離呢?
根據勻加速運動的公式:
在這里:V0=0;
所以,勻加速和勻減速階段的距離為:
就是加減速區域的三角形面積
同樣,恒速階段走過的距離是長方形的面積。
所以最終答案是:物體走過的距離是這個梯形的面積.
根據上述的分析,我們在進行位置控制時,首先知道的是需要運行的距離,及梯形的面積,然后我們可以根據實際要求設定加減速時間和最高恒速速度,這樣我們就可以計算出物體應該的速度曲線,然后我們控制變頻器驅動電機讓物體嚴格按照計算出的速度曲線去運行,就達到了位置控制的目的。
在ATV-IMC中的位置控制軟件完全按照伺服系統的方式設計和編寫。
具體流程參考圖5。

圖5 控制設計流程圖
首先我們通過"Profile Generator"功能塊計算出物體的運行速度曲線,然后控制變頻器按照速度曲線輸出,將位置傳感器反饋的位置值和參考位置值進行比較,PID運算,然后將PID運算的結果疊加到輸出速度上進行微調以增加位置控制的精確度。
3.3操作模式
此模塊的操作模式比較全:點動模式、回原點操作、給定位置停車、絕對位置控制、相對位置控制、受控停車、速度模式等。可以適合大部分場合的應用。
4應用案例
4.1長軌焊接基地起重機群吊項目
此項目使用了如下=S=變頻器產品:
標準變頻器ATV71: 0.75-3kW、380V、 64臺

圖6 長軌焊接基地起重機群吊現場
(1)技術要求
本項目由32臺3噸單梁起重機(固定小吊)組成。聯合吊運長鋼軌,一次吊運1 根。群吊月臺長度500 米,每臺小吊的距離約為16 米。在月臺的中部或端部設有控制室
小車運行速度為20米/分,小車跨度27米,起升速度為8米/分,最大起升高度5米。自動運行時,吊鉤的誤差不能超過30mm,32臺小車運行時需要保持絕對同步。
(2)解決方案
本方案采用ATV71變頻器開環控制小車電機,小車位置反饋采用自由輪加旋轉編碼器的方案,編碼器信號直接連接到CI卡上,PLC通過CANopen總線對小車進行控制;圖7為單臺小車的傳動方案。圖8為現場自由輪+編碼器。
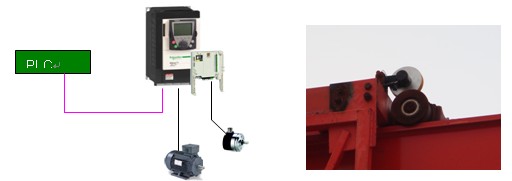
圖7 系統構成 圖8現場自由輪+編碼器
我們在每臺小車上都配置了上述系統,所以當32臺小車獲得運行的位置值時,他們計算出來的速度曲線是一樣的,這樣在正常情況下,32臺小車的運行應該是同步的,當有小車出現故障或不同步時,主PLC會干預處理,屏蔽掉該小車或調整速度,極端情況下全線停車。系統控制方案如圖9所示。

圖9 系統的控制方案圖
(3)控制效果
由于變頻器和小車電機之間為開環控制,速度精度較差;所以小車的位控精度最終在15mm,小于項目的技術要求范圍。
4.2全自動垃圾起重機
此項目將使用如下=S=變頻器產品:
標準變頻器ATV71: 15-160kW、380V、6臺

圖10 全自動垃圾起重機現場
(1)技術要求
起重機采用觸摸屏和可編程序控制器(PLC)進行半自動操作和程序控制。各機構驅動使用變頻器,根據工藝要求自動調整輸出頻率和電壓,實現起重機的手動和半自動運行。手動操作時在起重機控制室內能夠控制起重機移料、給料、堆料等所有動作;半自動操作時,在抓取完成后再根據所設定的投料地址,起重機在程序控制下,自動運行到投料位置,實現開啟抓斗,將爐渣投入到料斗中,自動完成投料過程。
由于全自動操作需要對料池進行區域劃分,自動定位,自動三維記憶等功能,所以既要求平移機構和起升機構能夠有準確的定位,由要求在給定位置到達后吊具不能有過大的晃動,影響工作效率,所以此機型為防搖控制和定位控制的結合應用。
(2)解決方案
我們使用ATV-IMC卡作為實際位控和防搖處理的控制元件,在ATV-IMC卡中我們將防搖和位置控制的功能聯合使用;及在高速段我們使用防搖功能來控制,位置控制為輔助功能,在低速段,主要使用位置控制功能。
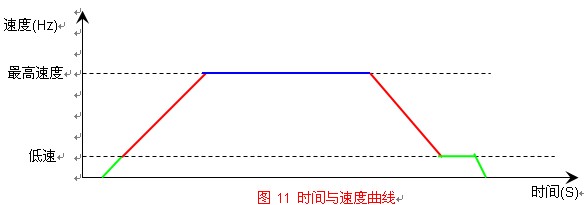
圖11 時間與速度曲線
如圖11所示,紅色的速度曲線為自動防搖激活的區域,綠色和藍色為自動防搖不激活的區域。對于定位來講,當起重機運行即將到達指定位置時PLC控制變頻器已最低速度運行(盡量的低速)。當位置到達時停車。
圖12為起重機的整體方案圖。
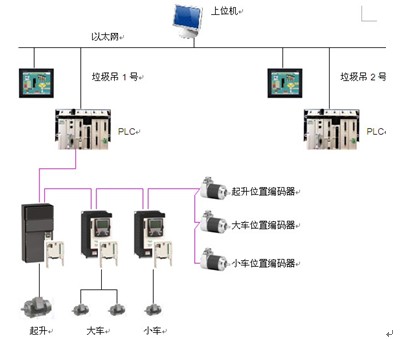
圖12 起重機的整體方案
所有機構都安裝帶CANopen通訊的絕對值編碼器,PLC首先獲取各編碼器的值,然后傳輸給相應的ATV-IMC卡。ATV-IMC根據運行模式進行實際控制。
5結論
利用ATV-IMC/CI作為控制單元來進行位置控制是變頻器功能的一個強大的延伸,由于ATV-IMC或CI可以直接安裝于ATV71變頻器上,所以這套系統具有不占用安裝空間,控制精度高,環境適應能力強等優點,能夠在起重行業得到廣泛的應用。